大家已经了解了法规对验证和确认的要求,但到底怎么执行应该还是比较茫然,因为质量管理体系的要求是非常宽泛的,要求的核心是为质量相关的过程建立程序文件,按程序文件执行,并留下相关的记录,后续持续改进。不管是验证还是确认,具体怎么实施,需要参考相应的指导文件,结合公司实际情况才能做出合理的方案。过程确认应该参考的文件是“国际医疗器械协调组织”发布的《质量管理体系-过程确认指南》下述讲的均是指南中的内容。 什么过程需要进行确认?指南中给出了一个决策判断流程,当过程输出可以验证,并且验证充分和经济时不需要确认,只需要验证和控制;当过程输出不可以验证/无法充分验证/不经济,并且风险较高时,需要过程确认并控制风险,或者重新设计产品或工艺;当上述过程风险非常低,也可以仅做验证并控制。 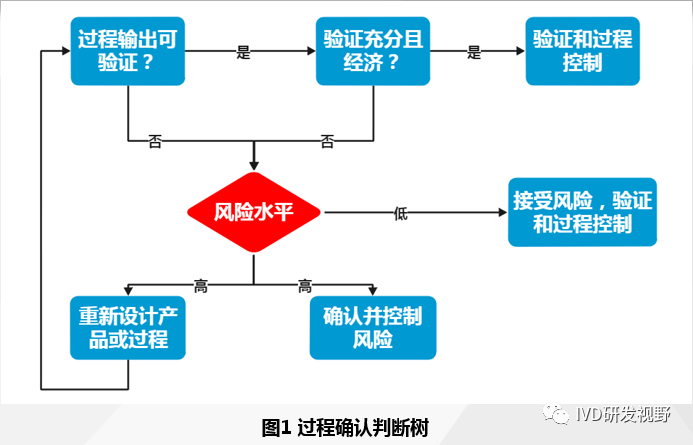
充分验证是指高度可靠地确认所有关键质量属性。 例如注塑过程,需要检查所有注塑件及所有关键质量属性。质量属于包含尺寸和强度,尺寸可以通过测量完全验证,强度需要进行抗冲击测试的强度测试,具有破坏性,无法完全验证,所以需要对注塑过程进行确认。另一个例子是手工切割过程,可以测量切割的所有尺寸,如果仅有尺寸这一关键质量属性,通过测量就充分验证了这一过程,只需要进行验证,不需要确认。第一类是需要进行确认的过程; 第二类是不需要确认可以充分验证的过程; 第三类是需要结合实际情况进行判断的过程。 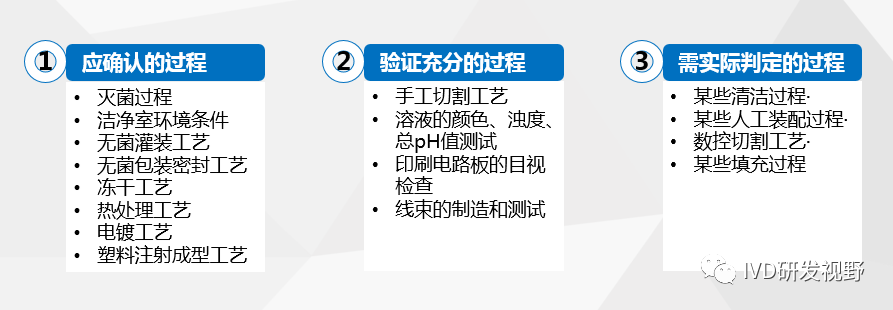 知道了哪些要做过程确认,很自然的就是什么时候做过程确认?法规对过程确认开始的时间没有要求,但是在法规里面要求成品放行前,需要完成DMR中所有活动,包括过程确认,意味着没有完成过程确认,不能放行成品。至于什么时候开始过程确认,审查机构建议在设计开发时就判定哪些过程需要确认,在设计转换时进行过程确认,因为这样就拥有实际生产的产品进行确认,同时可以解决因生产规模、设备设施、过程风险和潜在变更引入的问题。那怎么做过程确认?总共有8个步骤。 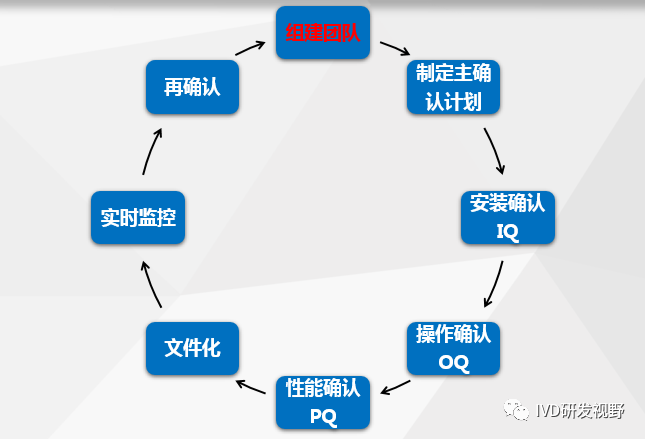 ——首先组建团队,团队主要由生产、质量、工程人员组成,同时还可以考虑其他相关人员加入。——成立了过程确认小组,下一步就是制定主确认计划,该计划包括以下内容:识别所需确认的过程,确认时间计划表,确认过程之间的相互关系,再确认时间安排。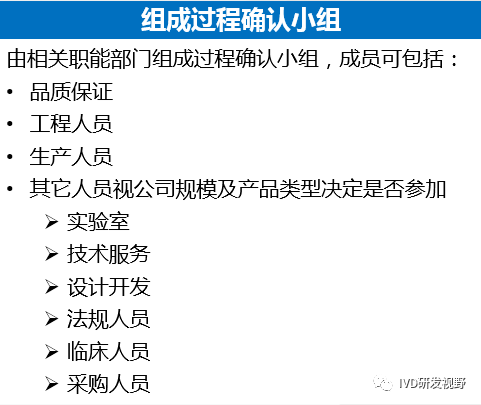 然后就进入了过程确认的三个关键步骤,安装确认、操作确认、性能确认。——安装确认的目的是确认设备是否正确安装,确保过程所使用的所有设备都符合既定规格,且设计、制造、放置和安装适当,便于维护、调整、清洁和使用,不产生不利影响(如影响环境):需要考虑设备设计特性、安装条件、校准、保养、清洁表、安全性、供应商随附文件、软件文件、备料清单、环境条件。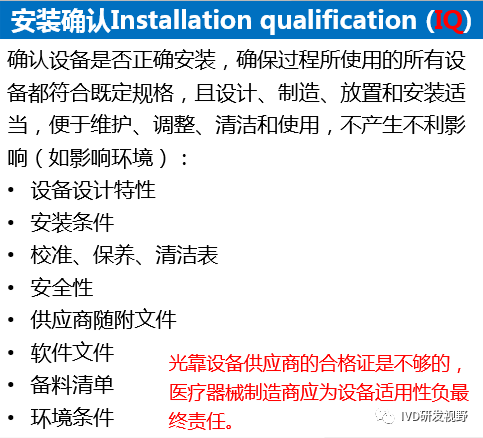 ——操作确认的目的是检验最差状况下过程结果的符合性,以确保这些设备在可预见的制造情况下均符合规定要求。对过程进行控制。应可以监测过程参数或产品特性,以允许过程在不同情况下均能调整,使其始终处于控制状态。应在过程确认期间,对过程所有可能出现的情况加以评估,并建立文件,以确保过程正常运行而避免不希望的事情发生。操作确认类似于我们熟知的室内质控控制,通过操作确认找到过程控制的失控界线、警告界线、在控界线、平均水平。作为后续过程监控的依据。 需要考虑的因素是过程控制的极限:如时间、温度、压力、速度等。软件参数、过程操作程序、原料规范、原料的处理要求、过程变化控制、培训、过程短期的稳定性和能力、潜在的失效因素,何时出现最差情况,何时采取纠正措施、应用统计技术建立关键的过程参数——性能确认的目的是是证明该过程在预期条件下,可以持续生产合格的产品。 可控因素包括:温度、湿度、电源供应变化、振动、光源、过程用水的纯度、环境、人员因素如培训、人机工程、体力等、原料的变化、设备磨损,即人、机、料、法、环五大方面。——完成3Q后,将过程确认计划、方案、结果、报告,再确认要求形成文件/记录归档。 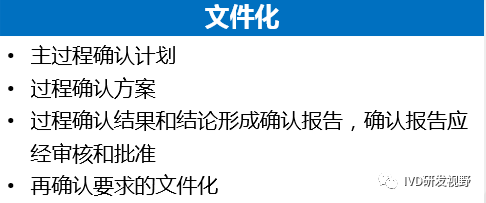
——完成过程确认后,根据过程确认结果形成日常过程控制和监控要求。 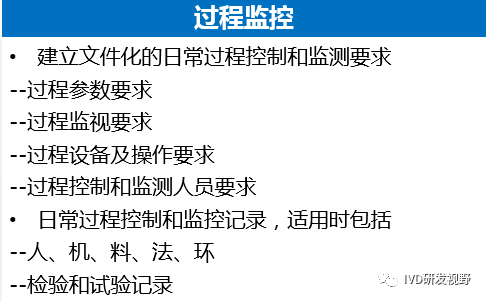
——当发生变更,产品质量有趋势性变化时,应进行再确认。 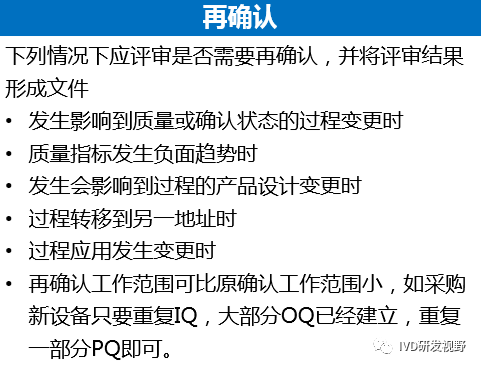
——回顾性历史数据也可以用于再确认。 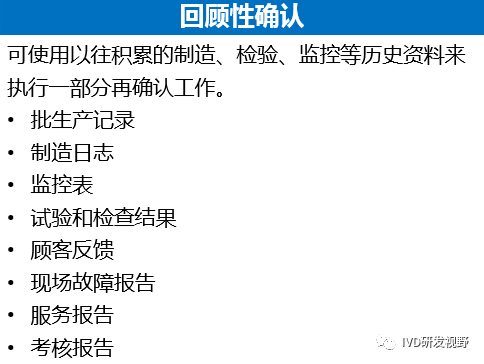
|